HMP Millsike construction complete
With the structural construction of HMP Millsike completed, PCE Limited’s HybriDfMA approach to prison design and build has set a new benchmark in the use of concrete elements.
PCE Ltd were appointed by lead contractor Kier as the superstructure and façade delivery partner for HMP Millsike, a category C prison accommodating around 1,500 inmates.
As part of the Ministry of Justice's New Prison Programme (NPP), HMP Millsike is the latest project to benefit from PCE’s advanced concrete construction techniques.
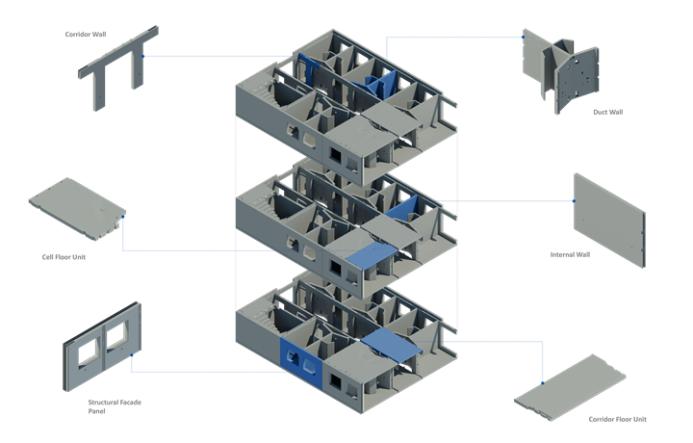
Design and Innovation
PCE’s Secure Prison system has been refined through the construction of over 10,000 secure cells.
The system employs a ‘kit of parts’ approach, featuring standardised concrete components such as sandwich panels, internal walls, circular and square columns, floor units, parapet walls, ground beams, and stair and landing units.
These components are crafted from a hybrid of reinforced concrete and steel, forming a robust superstructure.
The integration of M&E (mechanical and electrical) systems was meticulously planned within these concrete elements, using detailed model coordination and clash detection to ensure precision and quality.
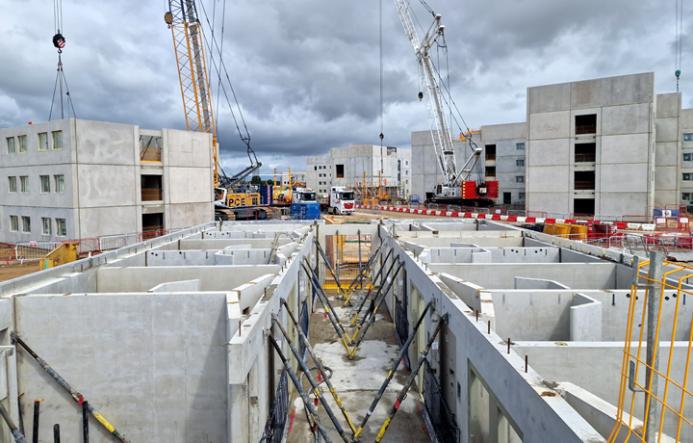
Manufacture
PCE’s flexible supply chain model selects the best offsite specialists for each project, ensuring top-quality concrete components. For HMP Millsike, nine specialist manufacturers across the UK and Europe were chosen based on structural integrity and performance. The collaboration defined high standards for aesthetics and tolerances, which were maintained throughout production.
Production began with the creation of nearly 13,000 hybrid components, weighing over 50,000 tonnes. To enhance efficiency, around 50,000 free issue castings were integrated during offsite production, including windows, door frames, underfloor heating mats, and shower components. Bespoke moulds were created for duct walls, corridor walls, and cell floor units, ensuring high precision and quality.
PCE’s offsite manufacturing approach ensures that concrete components are ready for installation upon arrival. Many of these components are finished to allow direct painting, reducing the need for additional materials and improving environmental sustainability.
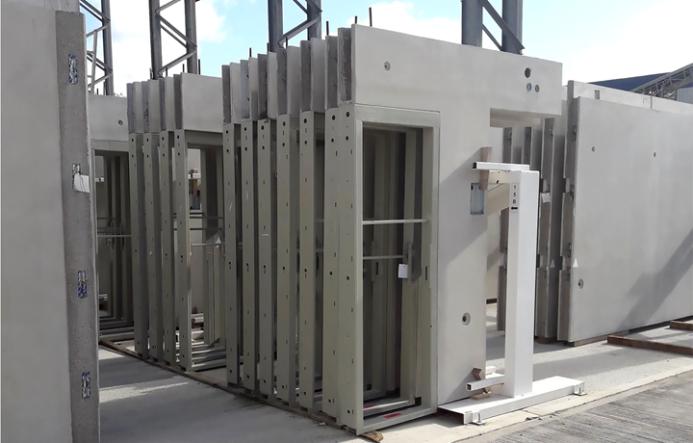
Assembly
The structural solution for HMP Millsike was completed 25% faster than the target period. PCE’s systemised offsite model significantly reduces onsite activity, deliveries, and disruption.
Standardised construction procedures and ‘smart connectivity’ enabled rapid assembly, with each houseblock structurally complete in just 12 weeks.
Teams of 13 operatives, including erectors, grouters, and finishers, provided a turnkey assembly solution, assembling up to 100 tonnes of hybrid material per day and achieving 200,000 RIDDOR-free hours.
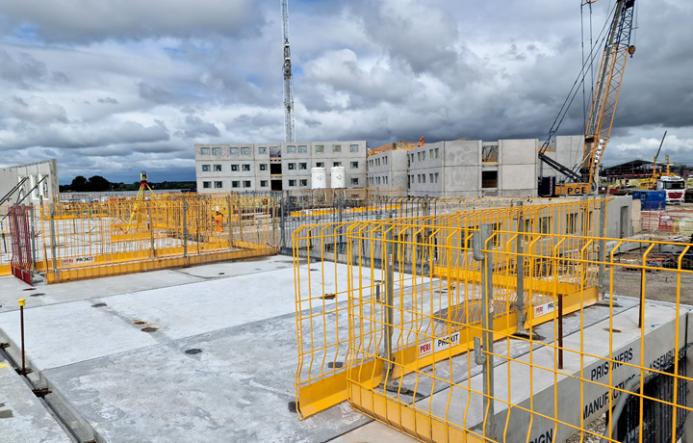
Logistics and Digital Integration
PCE managed the complexities of this large-scale project using advanced digital tools. The Ynomia digital asset tracking tool provided high visibility and real-time transparency, ensuring efficient collaboration and just-in-time delivery.
This digital integration saved over 5,000 hours and £300,000, projecting substantial cost savings for future projects in the NPP.
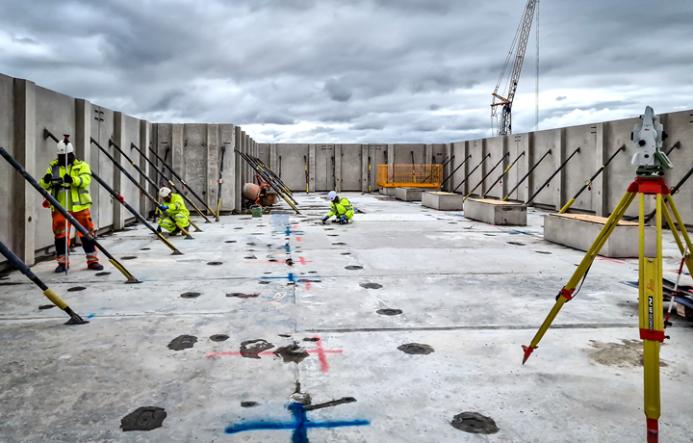
Community Impact and Social Responsibility
PCE is committed to community impact and social responsibility. The project team donated technology and equipment to local groups and employed ROTL (Release on Temporary Licence) prisoners, providing valuable construction skills and boosting confidence for post-release careers.
This aligns with the Ministry of Justice's goals to reduce reoffending.
Commenting on the completion of the project, a PCE Ltd spokesperson said: “Through its experience, continuous improvement, and innovative use of concrete elements, PCE has successfully implemented its Secure Prison HybriDfMA system for HMP Millsike.
“This approach ensures safety, speed, and scale while adhering to the highest standards of quality and compliance.”
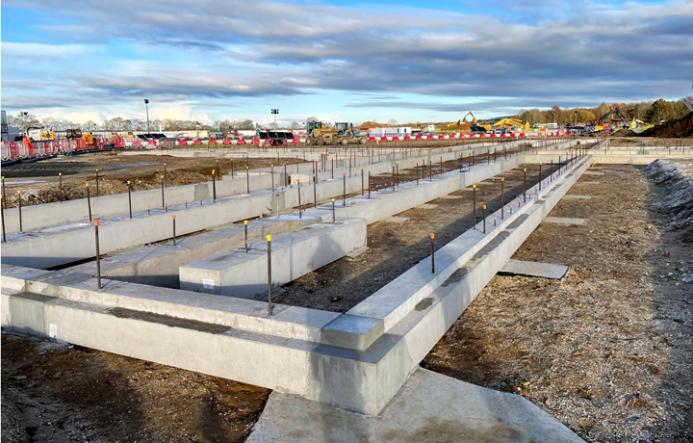