Paving with precision and durability
Concrete paving is uncommon in the UK but widely used in Europe for its durability on heavy-duty surfaces like motorways and runways. Wirtgen, a global leader in concrete paving equipment, has developed inset slipform pavers that streamline and perfect the concrete paving process. These pavers enable the construction of smooth, long-lasting surfaces with widths up to 16 metres and thicknesses of up to 450mm, designed to meet the demands of high-traffic areas and extreme durability requirements.
A typical Wirtgen inset paving process begins with concrete unloaded directly in front of the machine, which can then be spread by a belt conveyor or a placer/spreader, depending on project needs. This pre-placed concrete is then distributed evenly by a spreading auger or plough, with high-frequency vibrators ensuring even consolidation and removing any excess air from the mix. “Precision is key in creating surfaces that can withstand decades of use,” says Stefan Krebs, product manager for slipform pavers at Wirtgen. He adds that their equipment provides unparalleled control over concrete depth, form, and consistency as the paver moves steadily forward.
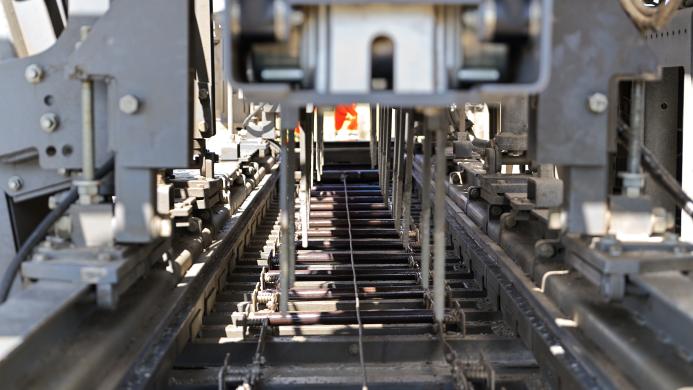
Wirtgen’s inset pavers also allow for optional dowel bar inserters that position reinforcement bars directly into the concrete according to the reinforcement plan. These bars help connect concrete slabs formed later, ensuring that natural cracking, caused by temperature fluctuations and heavy loads, happens along predetermined joint lines, which significantly improves durability and surface longevity. Additionally, tie bars can be inserted perpendicularly to strengthen connections between adjacent slabs. The oscillating beam that follows behind the mould fills any minor surface gaps, while a super smoother provides a second smoothing pass for further refinement.
Surface texture is an essential step in concrete paving, particularly on roadways. Wirtgen’s texture curing machines are designed to add a finish immediately after smoothing, applying a dispersion layer to prevent premature drying. These machines also produce textures with various materials, including brush marks, burlap cloth, or artificial turf, tailored to project requirements for grip and surface longevity. "From brush to burlap, we can deliver the right surface texture for the right grip," Krebs adds.
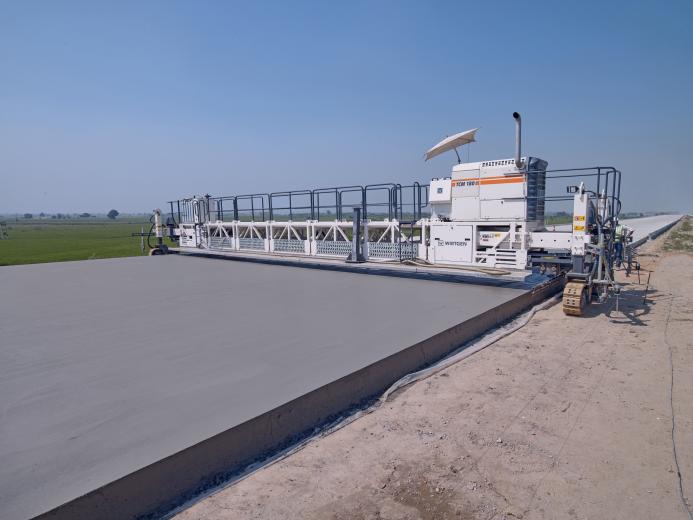
For projects that require thicker, two-layer concrete surfaces, Wirtgen offers both single-paver and dual-paver solutions. In single-paver two-layer paving, one machine handles both the top and bottom concrete layers simultaneously. For even weight distribution or larger sites, two separate machines can coordinate, each paving one layer in a synchronised, “wet-on-wet” approach.
Wirtgen’s pavers are built on rigid, torsion-free frames, ensuring consistently even surfaces without ridges or ruts, even across extensive projects. The machines use an advanced levelling and control system with options for both physical stringlines and digital controls like Wirtgen’s AutoPilot or 3D systems. Krebs explains that this approach guarantees precision from start to finish, producing a “perfectly even road surface” that can last 30 to 40 years, minimising both maintenance and resurfacing needs over its lifespan.
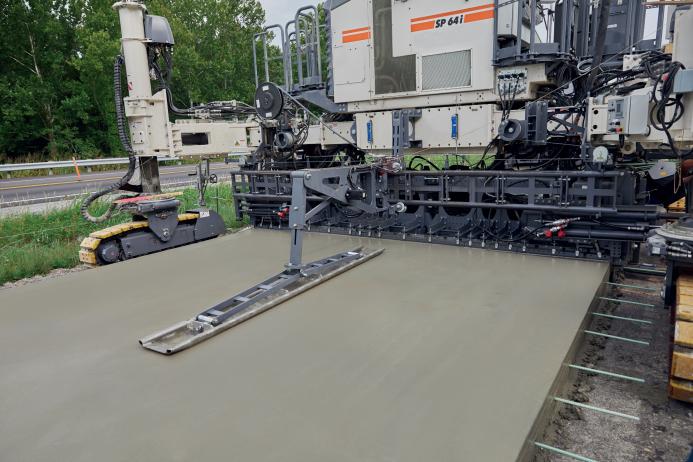