Video: Wendover Dean Viaduct deck complete
HS2 have successfully completed the installation of the 3,700-tonne deck for the Wendover Dean Viaduct in Buckinghamshire, employing innovative construction methods designed to reduce carbon emissions and improve efficiency.
The 450m-long viaduct, a key part of the high-speed rail link between London, Birmingham, and the North, saw its deck gradually slid into place over an eight-month period, from January to August 2024.
The installation involved assembling the deck in three sections, ranging from 90 to 180m in length. Each section was pushed from the northern end of the structure before the next section was attached behind it.
By the time the final section reached the southern end of the viaduct, the deck’s weight had increased from 590 tonnes at the start to 3,700 tonnes by completion.
James Collings, senior project engineer at EKFB, praised the team effort required to complete this complex task. “The final launch for the Wendover Dean Viaduct marks two years of collaboration and effort from EKFB and our supply chain partners. I’m proud of our progress and the team’s dedication to ensuring the safe delivery of this critical piece of infrastructure.”
To minimize friction during the slide, engineers used Teflon-coated pads between the deck and temporary steel bearings positioned on the viaduct’s nine piers, some of which stand as tall as 14 meters. The deck was also pushed slightly uphill, with the final resting position about 1.8 meters higher than the starting point.
With the deck now in place, the next stage involves lowering it by 60 cm onto its permanent bearings. This operation will take around two months, with the deck being lowered by 200mm at a time, pier by pier.
"It’s been fascinating to watch the deck slowly inch into position," said Nicola Henderson-Reid, HS2’s Head of Delivery. "We’re now moving into the next phase of the project, which involves lowering the deck into its final position and completing the remaining concrete work."
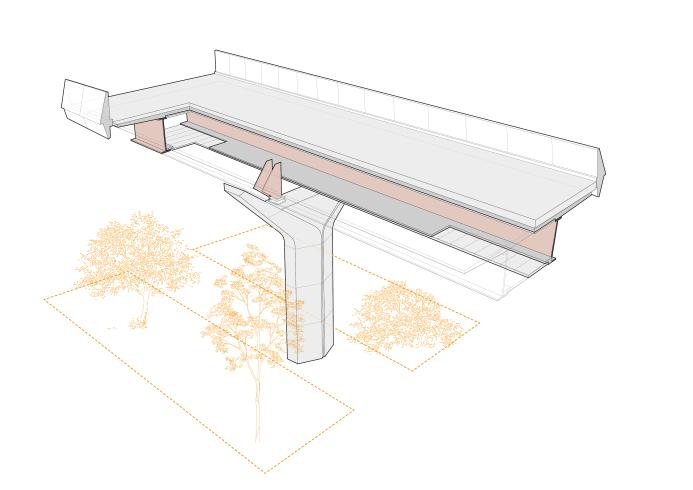
The double composite structure used in the viaduct has played a key role in reducing the amount of concrete and steel required. This innovative method uses two steel beams sandwiched between layers of reinforced concrete, providing strength while cutting the carbon footprint of the structure by around 50%.
“This approach not only makes the viaduct lighter and stronger, but it also helps us significantly reduce our environmental impact,” Henderson-Reid added.
Once the deck is fully lowered, work will begin on creating the concrete surfaces that will carry the railway tracks. This stage, expected to take around a year, will use specially designed traveling formwork that will move slowly from one end of the viaduct to the other.
The Wendover Dean Viaduct is the first major railway bridge in the UK to use this double composite structure, a technique inspired by high-speed rail projects in Europe. It is part of HS2’s commitment to modernize the UK’s rail infrastructure using sustainable and efficient construction practices.
The viaduct’s construction was led by EKFB, a joint venture of Eiffage, Kier, Ferrovial Construction, and BAM Nuttall, with pre-cast concrete shells for the piers manufactured in Northern Ireland to reduce on-site work and limit disruption to local communities.