New method to detect corrosion in concrete
New Method Detects Corrosion in Concrete Retaining Walls
A new method developed by ETH Zurich researchers can now detect corrosion in reinforced concrete structures, such as retaining walls, tunnels, and bridges. The technology is particularly useful for identifying corrosion in hard-to-reach areas, reducing the need for invasive procedures.
According to ETH Zurich, the innovation comes at a time when many concrete structures, especially those built between the 1960s and 1980s, are facing risks due to corrosion. As chemical changes in the concrete occur, the steel reinforcement can begin to corrode, potentially compromising the stability of the structure.
Lukas Bircher, a mechanical engineer working on the project, explained the challenge: "In the past, to check for corrosion in reinforced concrete, you had to remove concrete layers, which is time-consuming and disruptive. With our new method, we can assess the corrosion risk along the entire length of a retaining wall without removing a single piece of concrete."
The method uses electrochemical measurements to detect corrosion in reinforcing steel. A custom-designed probe is inserted into drainage pipes alongside a structure. Once the probe is sealed in place, water is pumped through the pipe to create an electrolytic connection with the steel reinforcement. The resulting electrical signals can indicate whether the steel is corroded.
"This technology allows us to measure the corrosion potential of the steel at various points along the wall," Bircher said. "It’s an early warning system, helping us identify areas that may need repair."
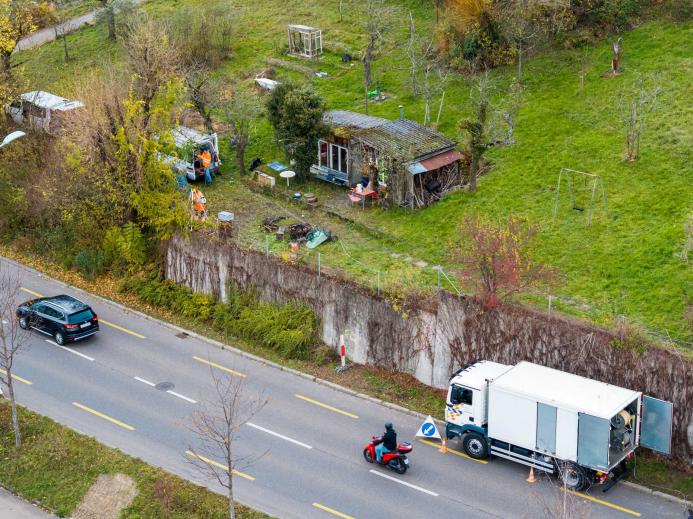
The team recently tested the method on the 200-metre-long retaining wall on Waidbadstrasse in Zurich-Höngg, which holds back tonnes of earth. The goal is to ensure the retaining wall remains structurally sound for many years to come.
Bircher noted that Switzerland alone has over 1,000 kilometres of retaining walls that may be at risk of corrosion, making early detection critical to maintaining safety. "By pinpointing the exact location of corrosion, we can focus repairs where they are needed most, extending the lifespan of these structures."
While the method has proven effective, Bircher and his team aim to automate the process further to reduce manual work and enhance the technology’s robustness. The team is now in the process of founding a start-up, Talpa Inspection, to commercialise their innovation. The name “Talpa,” inspired by the mole, reflects the team's ability to operate efficiently underground without the need for large-scale disruption.
Bircher’s team has already received backing from the ETH Pioneer Fellowship, which will help them bring the technology to market. The team is now in talks with potential customers, signalling strong demand for their solution.
“This method can save both time and money compared to traditional inspection methods,” Bircher concluded, adding that it can also reduce disruption on-site, making it an attractive option for infrastructure owners.
As the construction industry looks for ways to improve efficiency and reduce costs, technologies like Talpa's corrosion detection system offer a promising future for infrastructure maintenance and safety.