Slipform paving US Interstate 44 with Wirtgen's SP 94i
Capital Paving & Construction have used a Wirtgen SP 94i with dowel bar inserter (DBI) to pave parts of Interstate 44 in Missouri, US.
While slipform paving is not that common in the UK or Europe, it is the preferred method of laying concrete for the US's 46,747-mile (75232-km) long interstate highway system.
But, no matter where you are, working on any busy highway is always a challenge. Tight time frames and confined work areas force contractors to make the most of every square centimetre of working space, and working on the US interstate highway network is no exception.
As such, inset slipform pavers, such as the SP 94i, are popular in the US as they are ideal for producing large concrete pavements, including motorways and runways. Wirtgen’s SP series can pave roads and areas up to 18m wide between their crawler tracks, for example. The new SP 94i is a modular inset version with four steered and pivotable crawler tracks that can produce concrete pavements between 3.5 and 9.5m wide and up to 450mm thick.
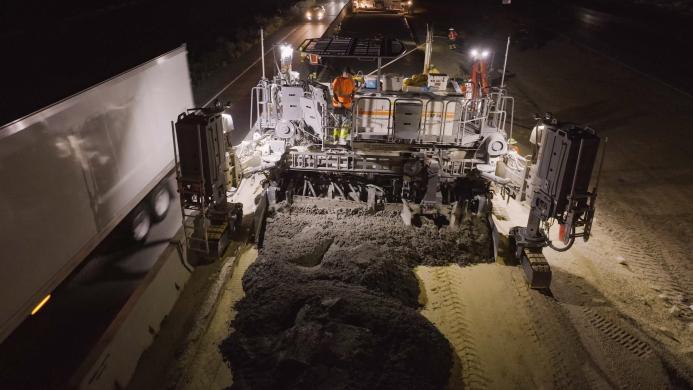
The optional dowel bar inserter (DBI), tie bar, and side tie bar inserter, as well as different slipform systems tailored to the regional requirements for inset applications worldwide, allow the SP 94i to be configured for a range of applications where high accuracy paving and intuitive and convenient operation are required.
To rehabilitate over 13 kms of lanes along the 1,025km-long Interstate, one of five built to bypass US 66, Capital Paving & Construction first removed the old concrete, then rebuilt the roadway in two sections using the SP 94i.
The first segment had a total width of 5.8m, and the second was 6.7m wide. Each consisted of a 3.7m-wide lane and an adjacent shoulder.
Access to the construction site on the interstate posed a major challenge, with trucks only able to unload the concrete directly in front of the machine, as there was not enough space to feed from the side. Choosing the right equipment was therefore essential.
“Instead of putting the basket out in front of the paver and tipping over the top of it from trucks, the DBI inserts the dowel bars right behind the mould,” said Tyler Kirchhoff, foreman, Capital Paving & Construction, “which makes it easier on the crew and easier for the tipper trucks to get back."
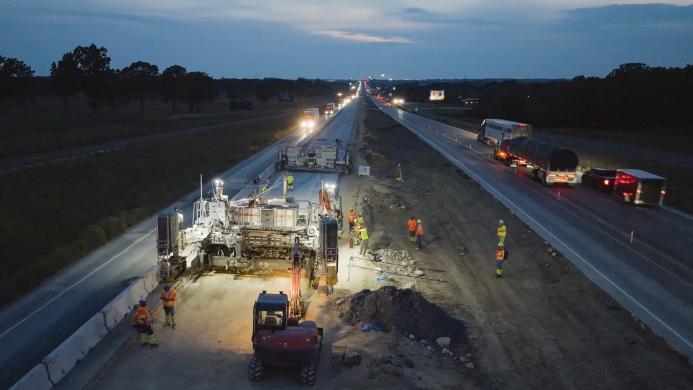
In addition to an increase in efficiency compared to paving with pre-placed reinforcement, a very high paving quality was achieved.
High productivity can only be achieved with machines that offer operators the simplest, most practical, and convenient operation possible. The simpler the control of the machine and the higher the degree of automation of the process, the more time the operator can spend processing the concrete itself. Even small improvements to the machine can majorly impact the overall result.
"What I like about this machine is the crows' nest. Our old machine didn’t have that, but this new feature lets me see our bar shooter in action and keep an eye on our vibrators. It provides a great overall view of what we’re doing", explained Brian Wood, machine operator.
When paving concrete, it is important to avoid any interruptions. To ensure a smooth process, the logistics and the paving team must be perfectly coordinated. In addition, the machine and all its components must be set up carefully on the construction site, with Wirtgen’s service and support team assisting.