Stringless machine control with AutoPilot 2.0
Wirtgen have introduced its AutoPilot 2.0 system, a stringless machine control technology that ensures exact paving results while reducing project costs.
The AutoPilot 2.0 system eliminates the need for traditional stringlines, using satellite-aided navigation instead. The system comprises a base station, a tablet computer, and an integrated control unit on the paver. This setup guides the paver along a virtual stringline, streamlining the paving process and enabling faster completion times.
"By removing the need for physical stringlines, AutoPilot 2.0 cuts down on setup and removal times, ultimately reducing overall project costs," a Wirtgen spokesperson said. "This system not only speeds up the workflow but also makes complex geometries, such as tight radii and S-bends, much easier to pave."
Slipform pavers, equipped with the AutoPilot 2.0, are used for a variety of monolithic concrete constructions using the offset method. This includes kerbs, gutter profiles, safety barriers, and cycle paths. Each project requires a specific slipform mould and process parameters, and Wirtgen's pavers offer the flexibility and adaptability needed for optimal results across a range of applications.
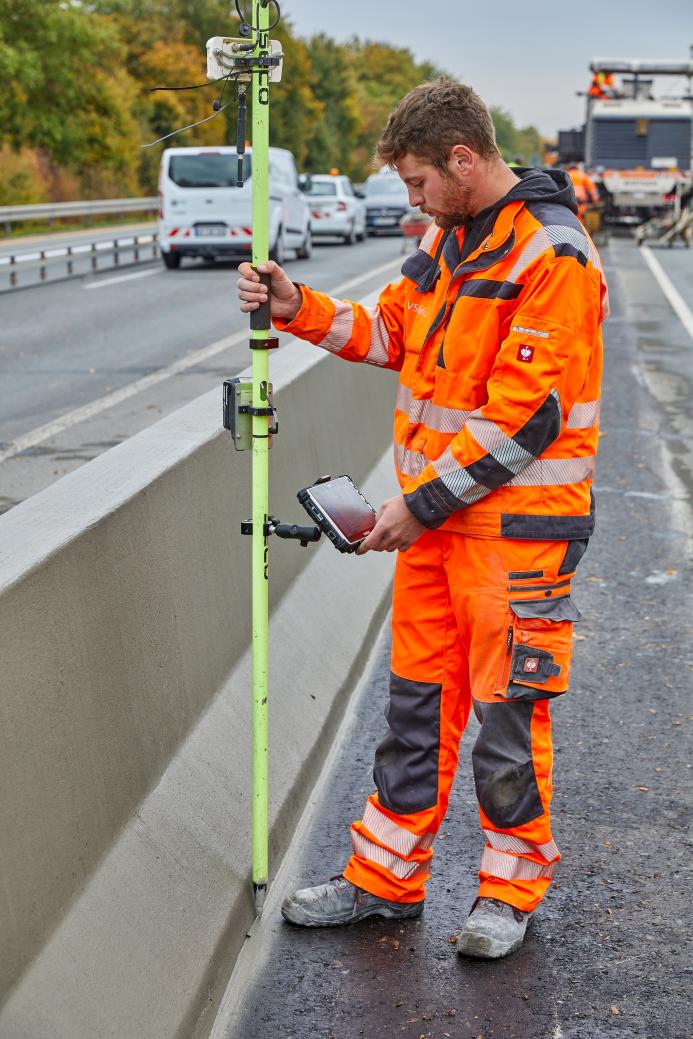
In offset paving, wet concrete is transferred from a mixer to the slipform mould via a feeding unit. As the paver moves forward, the concrete is compacted and shaped within the mould, producing a continuous profile with the desired shape. Wirtgen offers four models capable of paving widths up to 4,000 mm and heights up to 3,000 mm, along with numerous customisation options to suit different paving scenarios.
The modular design of Wirtgen's slipform pavers allows for a wide range of configurations, making them highly versatile and cost-efficient. These machines can be easily reconfigured for different applications, ensuring high utilisation rates.
Concrete feeding systems play a crucial role in maintaining a steady supply of concrete. Wirtgen offers both belt and auger conveyors. Belt conveyors can quickly move large quantities of concrete and are easy to maintain. They come in various lengths, including folding options for added flexibility. Auger conveyors remix the concrete during transfer, preventing material segregation. The feeding system's height, pitch, and lateral position can be manually adjusted on-site or from the operator's platform for quick adaptation to site conditions.
The slipform mould, a key component of the paver, is mounted on a height-adjustable and laterally telescoping suspension system. This allows it to be easily positioned on either side of the paver, facilitating paving in the direction of traffic flow. The mould can be relocated in just a few minutes with minimal effort.
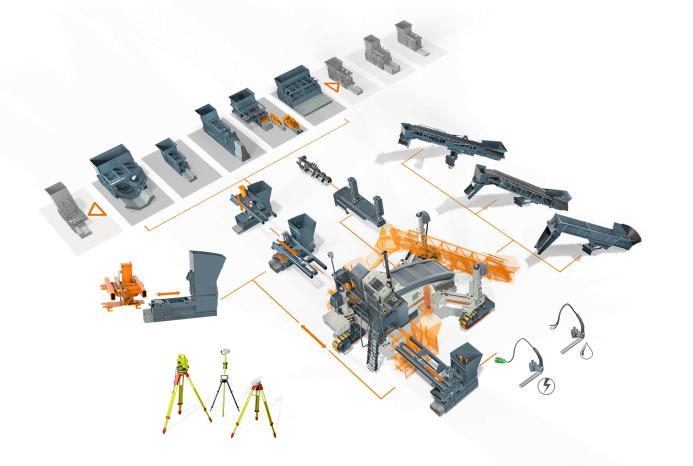
Legend:
1 Belt conveyor / auger conveyor
2 Flexibly adjustable concrete feeding system
3 Variable track unit positioning
4 Range of offset slipform moulds
5 Mould attachment right or left
6 Telescopic mould suspension
7 Mould quick-change system
8 Hydraulic or electric vibration
9 AutoPilot 2.0 stringless machine control
Wirtgen offers a variety of vibration systems for compacting concrete, including hydraulic and electric vibrators. A combination of both types can be used on the same machine to meet specific project requirements.
For maximum stability, the track units on Wirtgen's pavers can be flexibly positioned. Front track units with swing legs allow for adjustments in track spacing and lateral shifts. Some models also feature laterally telescoping rear track units, ensuring stability even in tight spaces or when paving with large offsets.
“Wirtgen's AutoPilot 2.0 system represents a significant advancement in slipform paving technology, delivering unprecedented precision and efficiency for construction professionals,” added a company spokesperson.