Wirtgen launch concrete milling solution
Wirtgen have introduced their new GENERATION C² round-shank picks, specifically designed for use with their ECO Cutter milling drums.
Offering a cost-efficient and sustainable solution for milling concrete, according to the company, the new GENERATION C² picks promise high resistance to fracturing, low wear, and long service life, potentially reducing operating costs significantly when removing concrete pavement.
Concrete is increasingly popular for road surfaces due to its durability. However, traditional methods for repairing or rehabilitating concrete pavement, such as breaking, excavation, and crushing, are laborious and costly. Concrete milling offers a more efficient alternative.
“The exceptional hardness of concrete presents a challenge to machines, milling drums, and cutting tools,” a Wirtgen spokesperson explains. “ECO Cutter milling drums are particularly suitable for removing large areas of concrete pavement. They have fewer round-shank picks with larger tool spacings, which increases the force applied by each pick. This leads to a higher machine advance rate and ensures higher area performance.”
Key features
GENERATION C² round-shank picks, when used with ECO Cutter milling drums, enhance construction profitability. The picks have a solid steel body geometry for better material removal, and optimised centring ensures that milling forces are concentrated in the top part of the holder, reducing the burden on the clamping sleeve.
The design also increases fracture resistance. Additionally, the grooved profile of the wear plate reduces wear and extends the service life of both the picks and the toolholders.
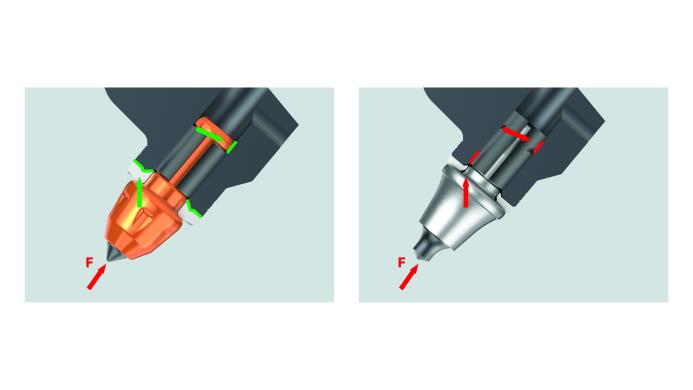
Sustainable and efficient method
Concrete milling is now an established technology globally. Technological advances allow for the efficient removal of almost all grades and hardnesses of concrete pavement.
This includes reinforced concrete with tie-bars, dowels, and steel rebar mats. Selective removal can separate concrete layers with different properties, reducing contaminated material.
“The method offers significant environmental benefits,” the spokesperson adds. “In most cases, the milled concrete can be recycled without further treatment. The vibration-free procedure also produces low noise and dust emissions, meeting all official building regulations and economic provisions.”