Concrete tech wins big at bauma 2025
Concrete-focused innovations recognised at bauma 2025 Innovation Awards
Innovations with direct relevance to the concrete construction sector were among the winners at this year’s bauma Innovation Awards, with several solutions showcasing the industry's move towards safer, lower-carbon and more efficient construction methods.
Among the top five winners, the VCT VARIOKIT Composite Track, developed by PERI and implemented by Adam Hörnig Baugesellschaft mbH & Co KG, won in the Building category for its role in transforming how steel composite bridges are constructed in in-situ concrete.
The innovation was first applied on the second superstructure of the Thulba Viaduct (video link), part of the A7 motorway between Fulda and Würzburg, Germany. This new formwork solution travels underneath the bridge, removing the need for conventional top-mounted carriage supports and allowing the carriageway slab to be cast without penetrations. This approach avoids cracking at the slab and cross-frame connections, improves surface quality, and significantly extends the service life of the structure.
The system also allows free access from above, meaning reinforcement and finishing work can be completed faster and more precisely using vibrating beams and finishing blades. Weekly cycle times are now achievable, reducing build time and lowering traffic disruption. According to Peter Wagner, head of bridge and civil engineering at Adam Hörnig, “We are never satisfied with the status quo. With this new cantilever bridge, we have the opportunity to improve our methods and advance the industry with innovation.”
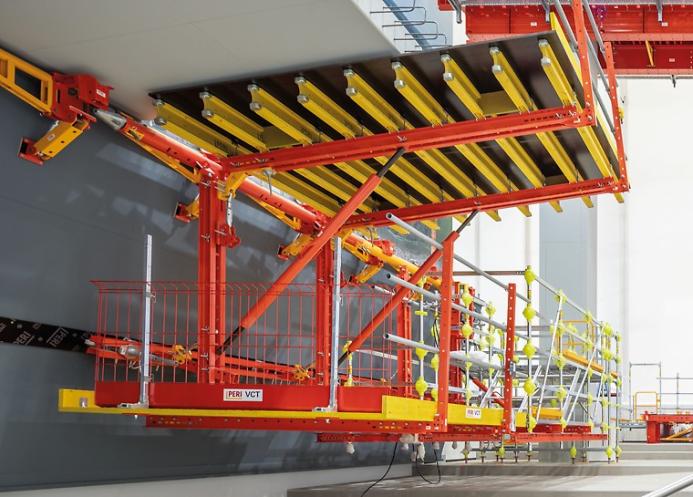
Tunnel tech and automation also awarded
The Tunnel Enlargement System (TES) (video link) from Herrenknecht, winner in the Mechanical Engineering category, was recognised for its ability to mechanically widen ageing railway tunnels while rail operations continue — a major technical and logistical achievement with clear implications for the concrete repair and sprayed concrete sectors.
Developed in partnership with PORR, the system is tailored to historic tunnels built during the 19th and early 20th centuries, many of which now require modern clearance profiles for updated rolling stock. TES uses a tunnel-in-tunnel method with a three-part modular system: a protective front shield, a middle working section equipped with telescopic drills, hydraulic hammers and shotcrete systems, and a rear logistics gantry.
This setup allows safe enlargement of tunnel cross-sections with minimal disruption to train services. For concrete professionals, the system’s integration of shotcrete application, reprofiling, and support arches demonstrates a high level of mechanisation in what has traditionally been manual and high-risk work.
The TES improves occupational safety through remote-controlled systems, fixed work platforms and enclosed work zones. It also minimises environmental disruption and planning delays by retaining the original tunnel alignment. The system has already proven itself in the field: two TES units are currently being used to upgrade the 426-metre Fachingen Tunnel and the 732-metre Cramberg Tunnel on the Lahn Valley Railway, widening both by over two metres while maintaining live rail traffic.
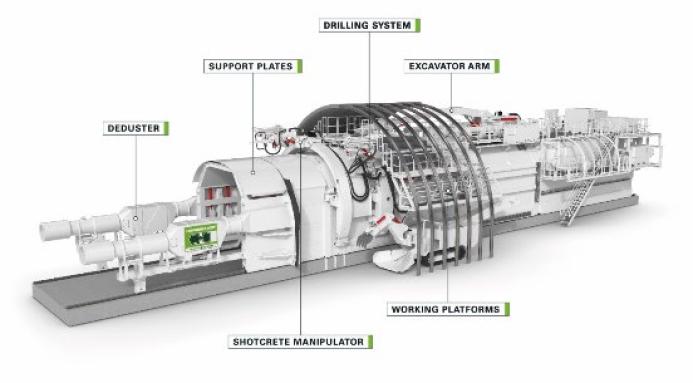
Autonomous site operations and carbon-smart curing
In the Digitalisation category, Liebherr won for its Autonomous Operations system — an advanced driverless platform for wheel loaders. Developed for monotonous or hazardous tasks, it allows for automated loading of hoppers, bulk material transport, and yard operations without operator intervention.
For the concrete sector, this innovation could significantly benefit quarry operations, batch plants, and precast yards, where repetitive handling of aggregates and materials is common. It operates without GPS, making it suitable for covered sites, industrial halls, or below-ground environments, and offers safer working conditions while improving consistency and reducing fuel and maintenance costs.
The Climate Protection award went to Robert Thomas, whose ROTHO ProCarbonCure (video link) system enables permanent CO₂ storage in concrete and steel slag products. The process has been successfully implemented at industrial scale and uses a closed-loop curing chamber that allows carbon dioxide to penetrate the material deeply without re-emission. This makes it a practical carbon capture, utilisation and storage (CCUS) solution for producers near major CO₂ sources.
The system features automated dosing and chamber aeration, a fully gas-tight structure, and multiple safety features developed through HAZOP analysis. For concrete producers, it offers a way to decarbonise precast production without major changes to product design or cement chemistry.
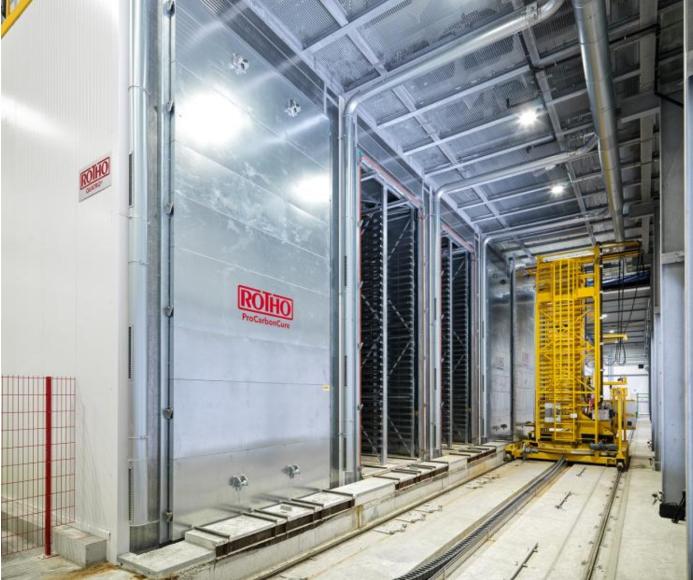
Scaffold-free refurbishment with robotic precision
In the Research category, the award went to the MAXX – Mobile Assembly X-System (video link), developed by Center Construction Robotics at RWTH Aachen University. MAXX is a plug-and-produce robotic platform for scaffold-free façade refurbishment, offering a practical solution for faster, safer upgrades to existing buildings.
Using a KUKA robot, 5G-enabled crane control, and a modular cable platform, MAXX autonomously installs façade elements such as Fundermax panels without requiring a building model or pre-programming. The system learns the layout from the first manually installed row and proceeds autonomously, adjusting in real-time to geometry changes — making it ideal for urban refurbishment, external insulation, or panelised concrete upgrades.
MAXX reduces labour intensity, improves site safety, and supports circular construction principles by making building reuse more attractive. While currently focused on façade installation, the system’s modularity and adaptability may allow future use in formwork positioning, precast mounting, or external cladding for concrete buildings.
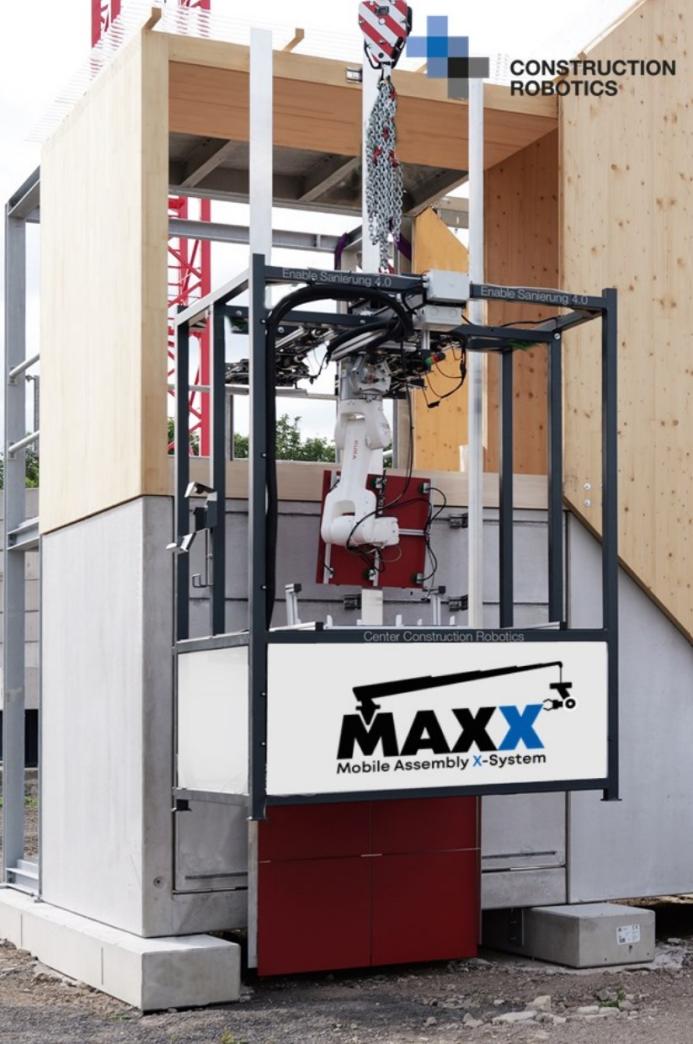
A strong future for innovation
The bauma Innovation Award is one of the construction sector’s most prestigious accolades. Held every three years, the 2025 edition drew 208 entries, with 52 finalists and five overall winners chosen based on sustainability, practicality, digitisation, and resource efficiency.
Speaking at the ceremony in Munich on 6 April 2025, Federal Minister Klara Geywitz and Bavarian Minister of State Hubert Aiwanger congratulated winners in front of 450 invited guests. The awards are jointly organised by VDMA, Messe München, and leading German construction industry associations.