Record-breaking pile installation
Balfour Beatty Ground Engineering (BBGE) has set a milestone at the Bridgwater GiGaFactory project by installing over 1,000 precast concrete piles in a single week, part of its work to support the UK’s largest electric car battery plant.
“It’s a great achievement for our project team, who really have smashed it out the park this week,” says Tom Cooke, operations manager at BBGE.
The Bridgwater GiGaFactory project, commissioned by Agratas (Tata Group), presents ambitious targets, with BBGE responsible for installing approximately 17,000 precast piles that will support the facility’s superstructure.
“Since we were appointed in July 2024, our 35-strong team has installed an average of 800 to 900 piles a week,” Cooke explains. “Breaking the 1,000-pile barrier shows the benefit of meticulous planning and collaboration with our in-house pile manufacturing facility in Nottinghamshire.”
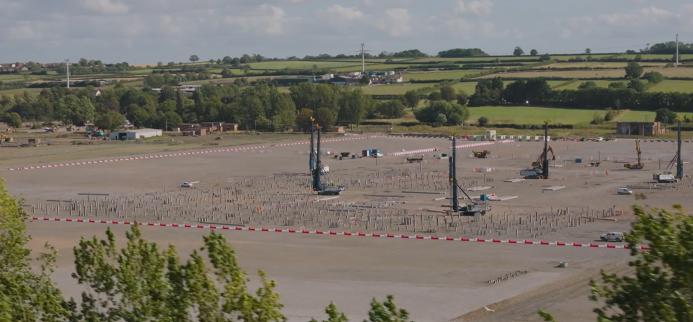
Advanced technology and precision logistics
BBGE’s approach leverages advanced logistics and technology to optimise the efficiency and safety of piling operations on-site. By using same-day delivery for precast piles, BBGE reduces the need for on-site storage, maintaining a clutter-free and safer workspace.
“The piles are only unloaded once and then installed, which helps keep the site clutter-free and reduces health and safety risks,” says Cooke.
The five Junttan PMx22 rigs selected for the project have played a critical role in meeting the high installation targets. Each rig is equipped with noise-reducing hammers, which limit sound disruption for nearby communities and reduce noise exposure for workers.
The rigs also include advanced ground-profiling software that continuously monitors and profiles soil resistance in real-time, enabling precise adjustments that enhance performance and reduce material waste.
“Understanding the ground conditions in detail helps us determine the most effective installation methods, optimising performance,” explains Cooke.
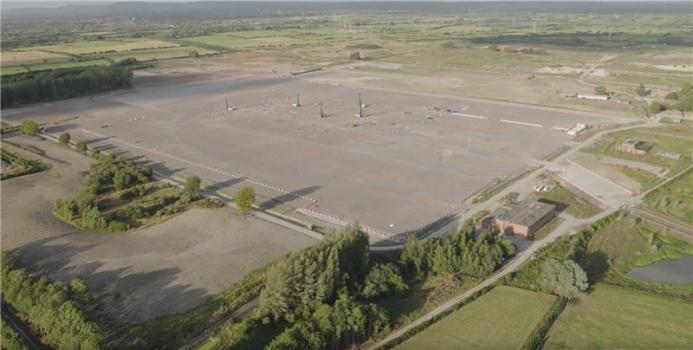
Unique terrain and environmental solutions
Working on the Somerset Levels has presented BBGE with specific environmental and geological challenges, including a high probability of flooding and a high-water table. BBGE’s early collaboration with Agratas and BBGE’s in-house environmental team helped establish tailored solutions to manage these site-specific factors.
“The terrain has a high probability to flood and a very high-water table, so a ‘wet concrete’ solution would have been difficult to construct,” Cooke notes. By opting for durable precast piles unaffected by groundwater, BBGE overcame this constraint effectively.
BBGE also worked with Agratas to establish a robust piling platform, essential given the area’s tendency to become saturated. This proactive approach included addressing potential bearing issues on the platform during the design and installation phases, ensuring safe operations despite the challenging terrain.
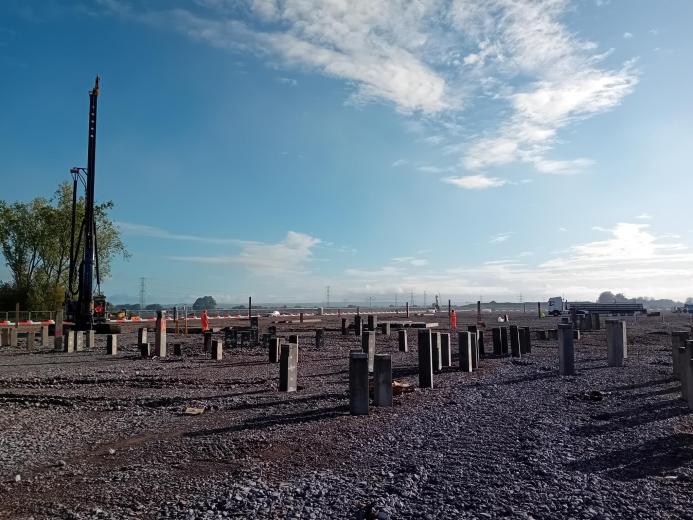
Sustainability and collaboration
Sustainability is central to BBGE’s approach at Bridgwater. By implementing displacement piling techniques—which compact rather than remove ground material—BBGE avoids traditional piling methods like Continuous Flight Auger (CFA) or Rotary piling. This approach reduces carbon emissions by minimising the need for lorries to transport arisings off-site.
“By compacting rather than removing the ground, we eliminated the need to transport arisings off-site, significantly reducing carbon emissions,” Cooke states.
The project team also benefited from local expertise and collaboration with BBGE’s Hinkley Connection Team, which previously installed 137 pylons in the area. Led by pre-construction director Rob Cannon, who has worked with the region’s geology since the mid-90s, the team integrated valuable insights from previous projects, helping to ensure efficiency and safety throughout the installation process.
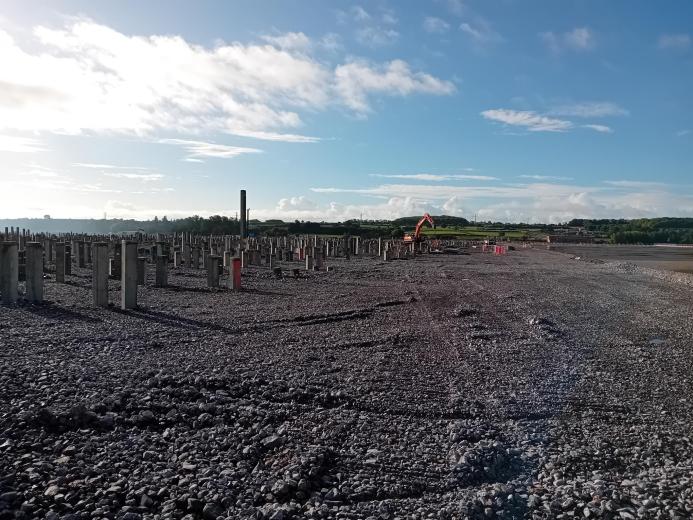
As of October 2024, BBGE has driven over 100,000 linear metres of piles, which is equivalent to stacking more than 220 Empire State Buildings end-to-end. With approximately 9,000 piles remaining, the project is on track for early 2025 completion, supporting Agratas’ plans for the GiGaFactory’s operational readiness.
“Our output on this multi-rig project is industry-leading. The efficiency of our Bottesford precast factory has enabled us to meet high delivery demands on site,” concludes Cooke. BBGE’s work at Bridgwater highlights its capability in delivering efficient, sustainable solutions for high-stakes projects, further strengthening its position as a leader in piling and ground engineering.