RBeam: A foundation system for modern construction
Roger Bullivant Limited (RBL) is setting new standards in foundation engineering with its RBeam Precast Ground Beam Foundation System. Designed for efficiency, adaptability, and sustainability, the RBeam system aligns with Category 3 Modern Methods of Construction (MMC) by integrating pre-manufactured components with advanced offsite manufacturing techniques.
The system has been deployed in a variety of residential and commercial projects across the UK, highlighting its flexibility in handling diverse ground conditions and its ability to meet modern construction demands.
A modular system built for versatility
One of the RBeam system’s defining features is its adaptability to different projects and soil types. At the Pirnhall Road development in Stirling, RBL paired RBeam with both 140mm driven steel tubular piles and 200mm driven precast concrete piles. This combination addressed the site’s shallow rock strata and soft clay overlays, ensuring robust and reliable foundations for the 104 homes and flats under construction.
"The flexibility of the RBeam system allows us to address unique ground conditions effectively," said Mark McAllister, foundation systems discipline manager at RBL. "By pairing the RBeam with both steel and precast piles, we can ensure stable and reliable foundations for a wide range of homes."
Similarly, at the Riverbrook Gardens project in Alnwick, RBL installed over 7,400 metres of RBeam and 1,800 piles to support homes on variable soils, demonstrating its scalability for large residential developments.
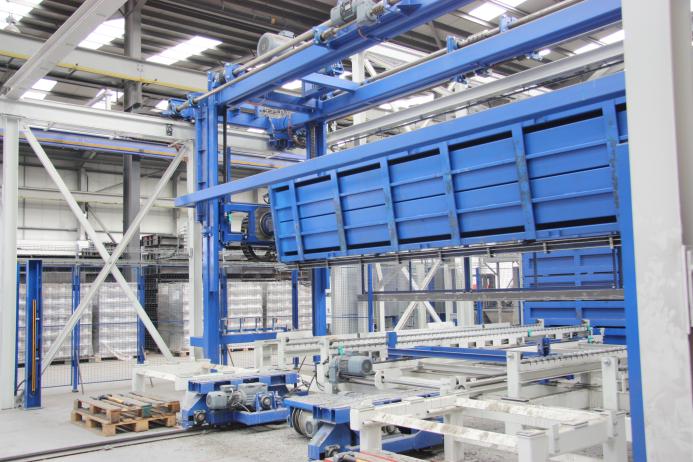
Precision through offsite manufacturing
The RBeam system is manufactured in RBL’s South Derbyshire facility, where controlled conditions ensure consistent quality. Each beam is cast using low-carbon concrete, a sustainable material designed to minimise shrinkage and cracking while reducing the environmental impact.
RBL can produce up to 4,500 metres of RBeam per week and maintains a stock of up to 10,000 metres, ensuring quick delivery to sites. The system’s modular design includes beams in multiple widths and lengths, offering flexibility while reducing lead times.
Speeding up installation
Once delivered, the pre-manufactured beams eliminate curing time and enable faster on-site installation. At the Killearn development in Scotland, RBL used 1,685 precast piles and 5,900 metres of RBeam to accelerate construction for 89 homes, showcasing its time-saving capabilities.
“The integration of driven precast concrete piles with RBeam highlights our commitment to innovation and efficiency,” said Gavin Hay, Scotland area manager at RBL.
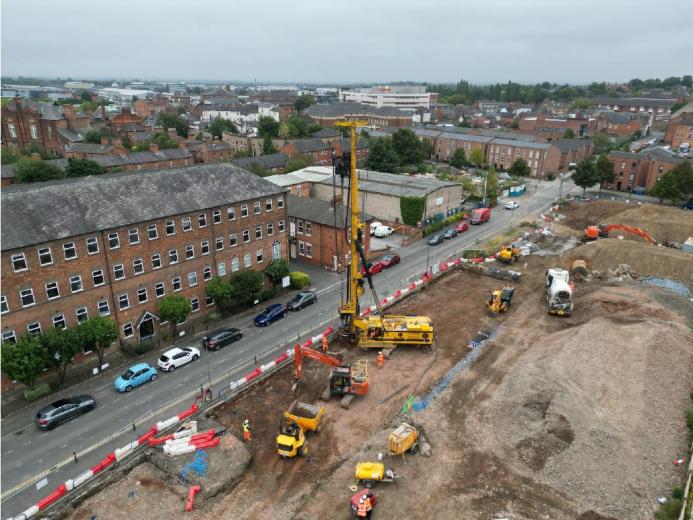
Meeting sustainability goals
Sustainability is central to the RBeam system. The use of low-carbon concrete and offsite production minimises waste and reduces vehicle movements to and from construction sites. These lean construction principles align with industry efforts to lower emissions and environmental impact.
This approach has proven successful in urban projects like the Castleward regeneration in Derby, where the combination of continuous flight auger (CFA) piles with RBeam minimised noise and vibration in a busy city centre.
Collaboration in action
RBL’s collaborative approach has been praised by developers across the UK. At the Stirling site, Dandara East Scotland Ltd highlighted the company’s ability to assist in design optimisation and ensure smooth project execution.
“The guidance and collaboration provided by RBL helped us manage costs and achieve a high-quality result,” said Brian Farmer, senior engineer at Dandara.
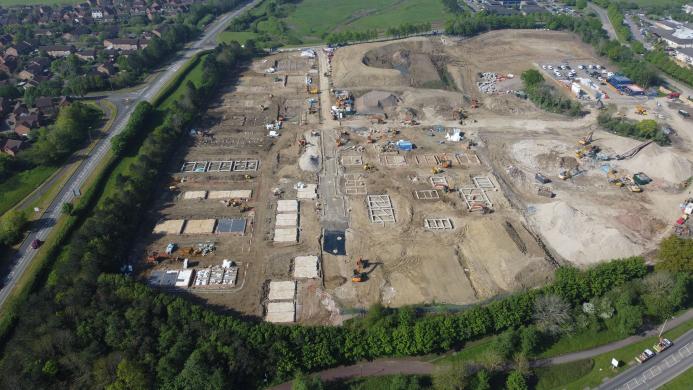
A system for the future
By integrating offsite manufacturing, sustainability, and adaptability, RBL’s RBeam system is setting a benchmark for modern construction. It provides a reliable, efficient solution for diverse projects, from suburban housing developments to urban regeneration schemes.
“Our focus is on delivering high-quality foundations that meet the challenges of modern construction,” said Phil Howard, Northeast foundation systems manager at RBL.
As the UK construction industry continues to embrace MMC principles, systems like RBeam are proving indispensable for projects that demand speed, sustainability, and reliability.
A look behind the scenes at how the RBeam system works…
Modern Methods of Construction (MMC)
RBeam is classified within MMC Category 3, premanufactured components. This brings efficiency, quality, and sustainability benefits to your project.
Offsite Construction
Components are made in a controlled environment, ensuring consistent quality and reduced delays. This allows for precise on-site installation, minimizes disruption, and lowers emissions.
Industrialisation
This reduces reliance on extensive skilled labour, enhances quality control, and leverages economies of scale, resulting in faster, more sustainable construction.
Lean Construction
This optimises efficiency by reducing material waste, ensures just-in-time delivery, and streamlines installation.
Platform Design
The modularity of the system allows it to follow a platform design approach as it can be used across different projects & sectors, improving scalability, lowering costs, and supporting faster project delivery.
Design for Manufacture & Assembly (DfMA)
RBeam’s design emphasizes standardized, simplified components that facilitate manufacturability and ease of installation.